Tipps für besseres Hardware Design
Motivation
Ich habe meine erste Anfrage für die Fertigung eines AnywhereAmps Alpha. Da ich nicht noch einmal 10h für den Bau aufwenden möchte, habe ich beschlossen, die Zeit in die Beschleunigung des Herstellungsprozesses zu investieren. Ich fand heraus, dass ich etwa eine Stunde pro Verstärker sparen könnte, wenn ich die Platine für mich herstellen lassen würde. Leider hat mich die Umstellung der Platine von manuellem Schneiden, Fräsen, Bohren und Löten auf ein PCB-Design doppelt so viel Zeit gekostet, als wenn ich sie bereits komplett gebaut hätte. Und ich weiß noch nicht einmal, ob das funktioniert. Aber fangen wir von vorne an.
Anforderungen an die neue Leiterplatte
Die Platine soll enthalten
- die Vorverstärkerschaltung, wie sie für AnywhereAmps Alpha entworfen wurde
- die Zwei-Wege-Weichenschaltung, wie sie für zukünftige AnywhereAmps Beta entwickelt wurde
- einen schaltenden Abwärtswandler zur Bereitstellung von 9V DC für Aux-Effekte
- eine Stromüberwachungsschaltung, die sowohl Batterie als auch Platine vor Überlastung, Kurzschluss, Unterspannung und Rückspannung schützt
Auf diese Weise möchte ich die Elektronik schrittweise professionalisieren. Ich beabsichtige, die gleiche Platine für alle Varianten der AnywhereAmps zu verwenden. Außerdem würde ich einige externe Komponenten loswerden, die ich von Hand herstellen und platzieren musste: Sicherung, hochstromfähiger Netzschalter, 9V-Regler und seine Kühlung, sowie einige Kabel.
Bauteilauswahl
Abwärtswandler
Ich habe im Internet nach einem Abwärtsschaltwandler mit geringer elektromagnetischer Interferenz (EMI) und einem Ausgang von
>1A
bei 9V
gesucht. Ein Linearregler hätte zwar weniger Störungen ausgesendet, aber bei einer Batterie-Nennspannung von 18V
hätte ich im schlimmsten Fall um 9W
thermische Verluste in Kauf nehmen müssen. Daher wäre diese Lösung überhaupt nicht batterieschonend gewesen. Ich entschied mich für ein (teures) Design, das alle notwendigen Komponenten in einem Baustein enthält, so dass ich nur noch das PCB-Layout richtig hinbekommen musste, um die EMI zu reduzieren. Ich fügte ein paar Bypass-Kondensatoren und einen Spannungsteiler für den Zielspannungs-Sollwert hinzu. Das war’s! (Dachte ich damals noch. So sah es tatsächlich aus)
Power Supervisor
Der einzige Schutz für meine Verstärker war bisher eine Sicherung, deren Wert auf den höchsten Betriebsstrom eingestellt war, den ich in den Schaltkreisen erwartete. In den frühen Prototypenphasen habe ich einige Operationsverstärker durch versehentliche Verpolung zerstört. Außerdem möchte ich vermeiden, dass der Akku völlig entladen wird, wenn ich vergesse, auf die Ladeanzeigen zu achten. Deshalb habe ich einen Power Supervisor IC ausgewählt, der Über- und Unterspannung und weitere Fehler erkennt und sowohl die Schaltkreise als auch den Akku vor Schäden schützt.
Gruppierung passiver Bauteile
Ich habe gelernt, dass die Herstellung einer Leiterplatte mit vielen verschiedenen Bauteilen teurer und fehleranfälliger ist als bei Verwendung weniger unterschiedlicher Bauteile, auch wenn ihre Gesamtzahl auf diese Weise steigt. Also habe ich viele Werte überarbeitet und die Simulation für den Audio-Vorverstärker mit diesen neuen Werten erneut durchgeführt. Schließlich gelang es mir, die Schaltung von 8/5 auf 3 verschiedene Widerstands- und 3 verschiedene Kondensatorwerte zu reduzieren!
Kondensatoren - mal wieder
Ich habe zunächst MLCC (Multilayer Ceramic Capacitors) in meinem Design verwendet, sowohl für den Bypass als auch für die Audio-Entkopplungskondensatoren. Nach erneuter Lektüre der Dokumente, auf die ich in meinem Beitrag preamp-design-considerations/ hingewiesen hatte, stellte ich fest, dass dieses Kondensator-Design Probleme mit Verzerrungen bei Audiosignalen zu haben scheint. Das Bild unten zeigt einen Vergleich verschiedener Kondensatortypen und -größen. Man erkennt, dass Folienkondensatoren hier am besten und MLCCs am schlechtesten abschneiden. Da ich keine Folienkondensatoren in der von mir benötigten Größe auf SMD-Basis finden konnte und Aluminium-Elektrolytkondensatoren zu groß waren, habe ich gepolte Tantalkondensatoren gewählt. Für die Bypass-Kondensatoren wählte ich low-ESR Typen.
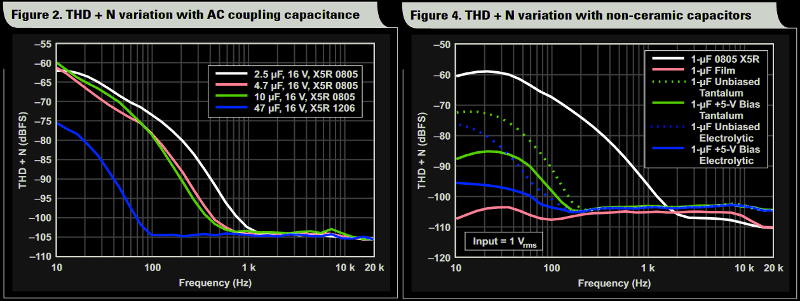
Schaltungsentwurf
Ich wählte die Open-Source-Software KiCad als Werkzeug zum Schaltungsentwurf und zeichnete alle meine bestehenden Schaltpläne neu, wobei ich die oben beschriebenen Komponenten hinzufügte. Man erkennt gut, dass der Verstärkerteil nur die rechte Hälfte des Schaltplans füllt, während die linke Hälfte der Stromversorgung und der Überwachungsschaltung gewidmet ist.
Ich habe versucht, die Schaltpläne so übersichtlich wie möglich zu gestalten, damit sie leicht zu lesen sind. Ich habe häufig globale Bezeichnungen verwendet und Steckverbinder zur einfacheren Montage hinzugefügt.
PCB-Design
Dies war der schwierigste Teil für mich. Ich habe noch nie eine Leiterplatte für Audioanwendungen entworfen, also musste ich eine Menge Richtlinien lesen, bevor ich anfing.
Anleitungen und Tutorials
Ich liste einige davon unten zur Information auf:
- Rauschen auf Leiterplatten und wie man es vermeidet
- Wie man Bypass-Kondensatoren am besten platziert
- Massefläche oder nicht?
- Wie man verschiedene Massen für Signal, Stromversorgung etc. verbindet
- Bauteilpositionen für den Lötvorgang optimieren
- Übliche Probleme beim Platinendesign
- Wie viel Strom kann ich über welche Leiterbahn schicken?
- PCB Design Tipps für die maschinelle Fertigung
- Tipps zur reduktion der Störanfälligkeit bei eigenen Platinendesigns
AnywhereAmps PCB erklärt
Das Ergebnis nach ein einigen Stunden Arbeit:
Die Platine ist in zwei Lagen vollständig geroutet.
Ich habe die Leiterplatte in drei Bereiche unterteilt.
- Links: der 9V-Schaltregler, der seinem Referenzdesign (Datenblatt) folgend mit Hilfe der Bypass-Kondensatoren einen Stromkreis um sich selbst bilden und den größten Teil der elektromagnetischen Störaussendung auslöschen würde. Das thermische Design, lässt viel Platz für Kupfer und einige Durchkontaktierungen, sodass die Wärme vom Chip gut abgeführt werden kann.
- Mitte: Die Stromanschlüsse und die Überwachungsschaltung. Ich habe Lötbrücken gesetzt, um die Nennspannung der Batterie für die Unterspannungserkennung auszuwählen.
- Rechts und oben: Vorverstärker und analoge Signalschaltung, getrennt von der übrigen Elektronik durch eine dicke Massebahn auf der oberen Ebene und eine eigene Massefläche auf der Unterseite. Ich hoffe, das ist genug.
Da ich die ersten Prototypen von Hand löten werde, um zu prüfen, ob alles gut funktioniert, habe ich “große” 0805 SMD-Bauteile verwendet. Ich habe den Abstand zwischen den Bauteilen größer gemacht, als es die PCB-Spezifikation verlangt. Leider waren die hochintegrierten Leistungs-ICs nicht in “Hobby-Löt-Elektronik”-Größen erhältlich, so dass ich hier noch einige Mühen auf mich nehmen muss.
So wird es also aussehen. Die Leiterplatte wird 45mm x 69mm groß sein.
Herunterladen oder eigene Beiträge erwünscht?
Alle meine Zeichnungen in CAD sowie Stromlaufpläne sind quelloffen und zum Download auf meinem eigens dafür angelegten Github Repo verfügbar.
Nächste Schritte: Platinen geliefert und verlötet