Dibond Tests
Anmerkung: Die in diesem Artikel analysierten Gravuren sind recht fein. Die Schrifthöhe beträgt zwischen 3 und 6mm, und die Größe des Werkstückes liegt bei 80x80mm. Blickt man von einer Distanz von 30cm oder mehr auf das Werkstück, so sind die rauen Kanten etc. nicht mehr wahrnehmbar.
Weitere Qualitätsverbesserungen bei Arbeiten mit Dibond
Die in meinem letzten Fräsprojekt in Dibond erzielten, nur mittelmäßigen Ergebnisse wollte ich so nicht auf mir sitzen lassen. Deshalb habe ich mögliche Einflussgrößen ersonnen und niedergeschrieben.
In diesem Artikel versuche ich, sie Stück für Stück zu analysieren und schließlich, falls erforderlich, auszuschalten.
Mögliche Gründe für schlechte Qualität
- Verschlissene Fräser
- Falsche Schneidengeometrie
- Ungeeignete Parameter
- Gleichlauf statt Gegenlauf
- zu geringe Gravurtiefe
- zu hohe Gravurtiefe
- Maschinenvibrationen
- Fräsmotorhalterung zu weich
- Unwucht
Untersuchung der Fräser
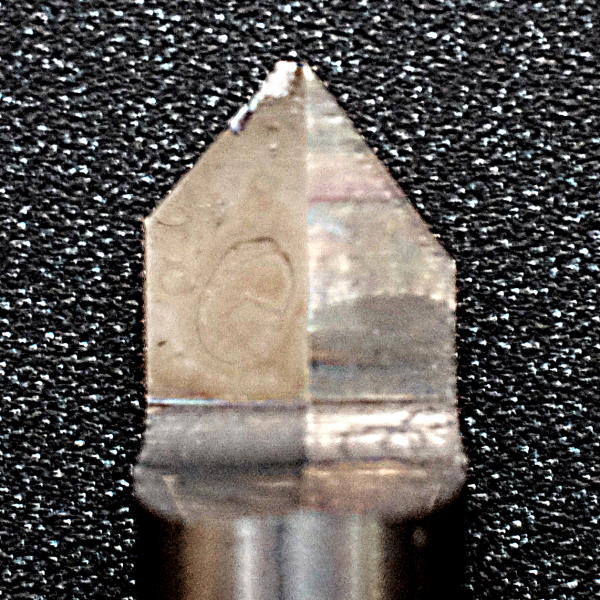
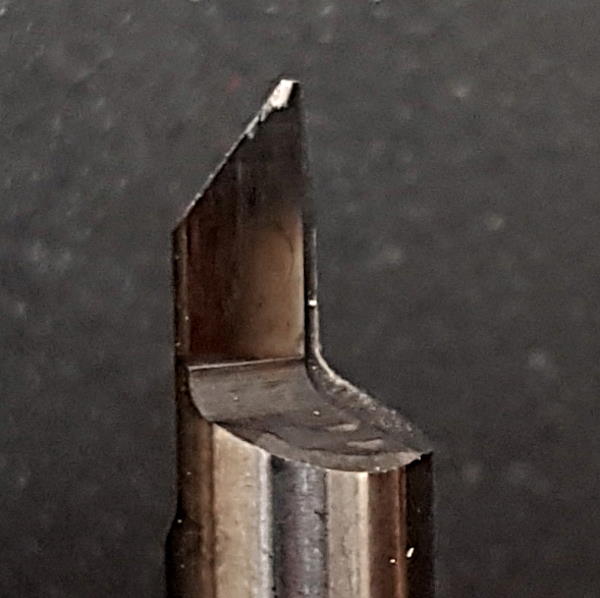
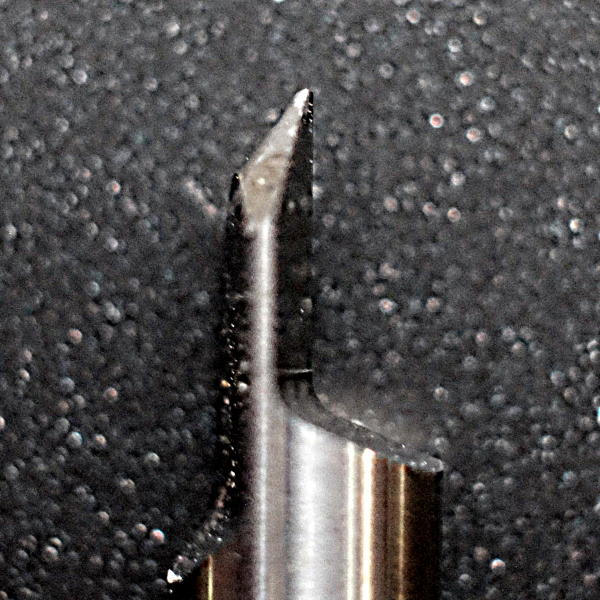
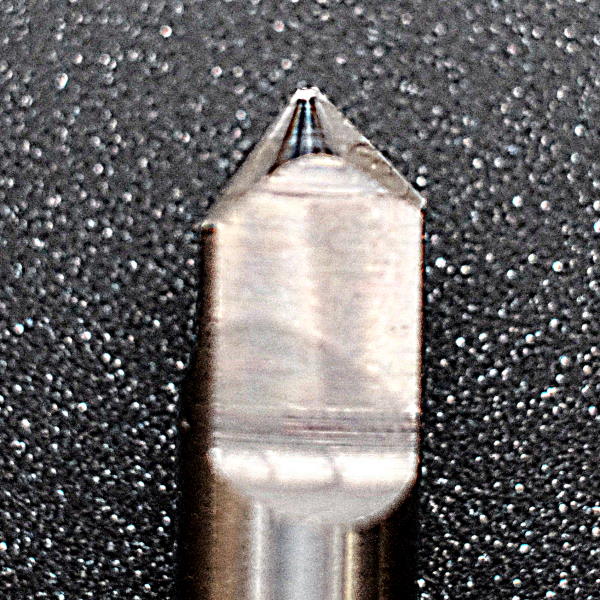
Ich bin kein Fräserexperte, aber ich kann mir kaum vorstellen, dass ein VHM-Fräser nach nur dreißig Arbeitsminuten in Kontakt mit 0.3mm
starkem AlMg1
stumpf sein soll (Na gut, da mögen ein paar Zusätze drin sein für die gebürstete Oberfläche samt Färbung). Die Schneiden sehen recht sauber aus. Das Einzige, was mir auffällt, ist eine dünne Schicht Aluminium, welche der Schneide anzuhaften scheint.
Diese habe ich vorsichtig mit einem Cuttermesser entfernt. Nun sehen sie wieder normal aus.
Update Okt-23: Ich habe mit denselben Graviersticheln - Sie sind inzwischen ca. 4h gelaufen - etwas in Acrylglas (PMMA) gefertigt. Die Schnittkanten sind hier rauer als bei brandneuen Gravierfräsern.
Schneidengeometrie
Die für diesen Test verwendeten Fräser haben keine Spiralnut zur Spanabfuhr, sondern sind auf der Eingriffseite offen ausgeführt. Daher ist aber auch stets die komplette Schneide im Eingriff und ich frage mich, ob das einen Unterschied macht. Vielleicht wäre eine gewundene Schneide (Habichtschnabel, Helix) hier besser geeignet?
Hintergrund dieser These ist, dass mein CAM-Werkzeug für Gravuren keine Pendelbewegung oder Helix zum Eintauchen verwendet sondern stets gerade in das Material eintaucht. Wenn man bei den Bildern unten (z.B. in der Vergrößerung des t
) genau hinsieht, so erkennt man Kratzer im Klarlack, wo der Fräser ins Material eingetaucht ist und die Späne nicht hat rechtzeitig abführen können.
Auf der anderen Seite werden spiralgenutete Fräser das Material nach oben ziehen. Da das Aluminiumblech lediglich thermisch mit dem PE-Kern verklebt ist, könnte die Haltekraft besonders bei filigranen Gravuren durchaus zu gering sein und sich die Aluminiumschicht ablösen - die Gefahr ist besonders hoch bei Inseln, wie es sie z.B. bei den Buchstaben e, a, o, g, p...
gibt.
Kurzgesagt TODO: Gravierfräser mit Spiralnut kaufen, ausprobieren und die Fräsergebnisse hier dokumentieren
Ungeeignete Parameter für Vorschub und Drehzahl
Ich habe die empfohlenen Parameter nochmal geprüft, mit dem Hersteller der Fräser besprochen und sie auch in ein paar Berechnungstools eingegeben. Optimalerweise werden sie bei noch höherer Drehzahl als 24000U/min
betrieben, was an meiner Maschine allerdings das Maximum ist - also behalte ich das so bei.
Also bleibt mir jetzt noch der Vorschub zum Herumspielen übrig. Schnell eine Testgravur im CAD erstellt und im CAM dann mit verschiedenen Vorschüben abfahren lassen: F600mm/min
, F800mm/min
sowie F1000mm/min
.
In diesem Bild kann man viele Dinge erkennen:
- Die Beschriftungen für verschiedene Vorschubgeschwindigkeiten sind so klein geraten, dass der Gravierstichel nicht einmal die Aluminiumschicht vollständig durchbricht. Vielmehr quetscht er das Aluminium in die darunter liegende Polyethylenschicht und zur Seite weg.
- Obwohl ich die Vorschubgeschwindigkeit um bis zu 20% pro Umdrehung verändere, bleibt die Schnittqualität gleich. Dies bestätigt, dass für meinen Stichel in Dibond ein Vorschub von
F1000mm/min
in Ordnung ist. - Es ist deutlich zu sehen, dass die äußeren Kanten der Gravur rau sind. Ich kann dies fühlen, wenn ich mit dem Finger über das Werkstück streiche.
- Die inneren Ränder der Gravuren sind wirklich glatt. Sie glänzen im Gegensatz zu ihren matten Gegenstücken.
- Die schwarzen, inneren Teile der Spirale sind sehr gleichmäßig und ohne Schnittspuren gefertigt.
- Das große
T
des Wortes “Test” sieht etwas seltsam aus, da senkrechte Kerben an der Schnittkante auftreten. Darauf kommen wir später noch zu sprechen.
Kurzgesagt: Drehzahl- sowie Vorschubparameter sind OK und scheinen für mein Problem nicht die Ursache gewesen zu sein.
Gleichlauf- vs. Gegenlauffräsen
Um zu entscheiden, ob es bei der Verarbeitung von Aluminiumsandwichplatten eine bevorzugte Fräsrichtung gibt, schauen wir uns die Spirale etwas genauer an:
Die schmalere Linie wurde in einem Schritt gefertigt während die breitere einen zweiten Durchlauf mit nur Z-0.1mm
Tiefenzustellung hat.
Sofort ist zu erkennen, dass die Gravur außen viel glattere Kanten hat als innen. Die Spirale wurde von außen nach innen mit einer rechtsdrehenden Spindel gefräst.
Das bedeutet also, dass außen im Gegenlauf und innen im Gleichlauf gearbeitet wurde.
Kurzgesagt wird auf einer CNC zwar eher der Gleichlauf empfohlen, bei der Bearbeitung von Dibond ist unter Verwendung von Graviersticheln jedoch im Gegenlauf mit deutlich besseren Ergebnissen zu rechnen.
Zu niedrige Gravurtiefe
Wie die Bilder oben zeigen, sollte die Aluminiumschicht beim Gravieren satt durchbrochen werden. Nach ein paar weiteren Tests konnte ich die minimale Gravurtiefe bei 0.3mm
Schichtstärke des Blechs bei etwa 0.5mm
ermitteln.
Zu hohe Gravurtiefe
Diese Mutmaßung ergab sich bei meinem vorigen Experiment mit Dibond. Zum Vergleich habe ich hier zwei verschieden Dicke Gravurpfade gefertigt. Tiefere Gravuren werden tatsächlich etwas sauberer, wenn man sie mit einem Schlichtgang nochmal nachzieht. Für schmale Gravuren halte ich die Verbesserung für vernachlässigbar. Daher ist eine Hohe Gravurtiefe meiner Einschätzung nach kein Problem.
Vibrationen
Betrachtet man erneut die Kerben und Unregelmäßigkeiten an der Schnittkante, so liegt der Schluss nahe, dass sie sich aus der gebürsteten Oberfläche ergeben. Tatsächlich nämlich wird die Oberfläche aber nicht gebürstet, sondern unter hohem Druck mit Hilfe von Walzen geprägt. Die Kerben könnten also durch Dichteunterschiede im Material begünstigt werden. Es gibt aber eine weitere mögliche Ursache: Maschinenvibrationen.
Die Texte wurden mit verschiedenen Vorschubwerten gefertigt. Die Zahlen geben hierbei den Vorschub an: 6
bedeutet 600mm/min
und so weiter. Ich habe noch ein weiteres Bild gemacht, was die Buchstaben nochmal stärker vergrößert darstellt. Hier zeigt sich, dass die Texte bei größerem Vorschub ein klein wenig besser aussehen.
Im letzten halben Jahr habe ich viel mit den mechanischen Werten der Maschine experimentiert, um die Grenzen auszuloten. Ich habe damals recht hohe Werte für Geschwindigkeit und Beschleunigung festgelegt, da ich die Maschine für fähig hielt, diese zu unterstützen. “Unüblich hoch” nannte der Hersteller der Steuersoftware diese Werte, als ich ihn wegen eines anderen Problems kontaktierte (“Velocity was higher than max!”).
Also habe ich ein weiteres Teststück designt, wo ich nur gerade Linien und Texte gravieren würde, sodass rechtwinklige Ecken entstehen an denen die Maschine auf null abbremsen und von dort wieder beschleunigen würde.
Dieses mal habe ich den Vorschub bei F1000mm/min
belassen, aber in jedem Durchgang die Beschleunigungswerte der Maschine verändert.
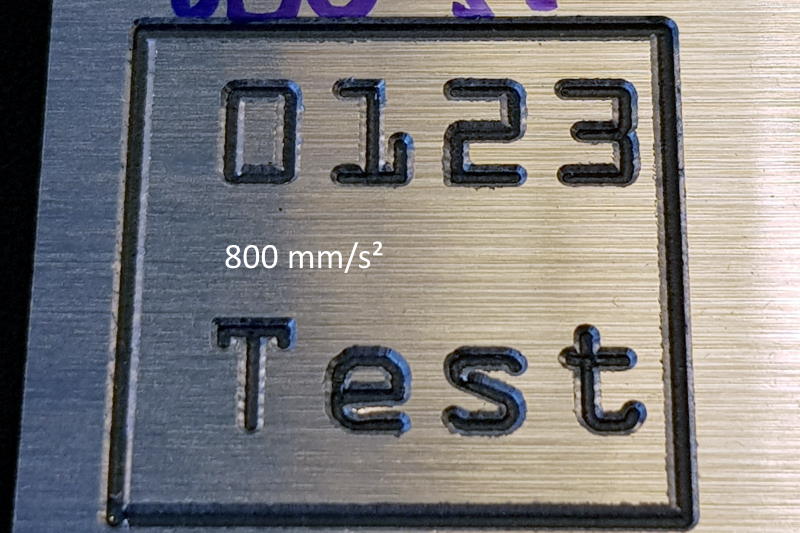
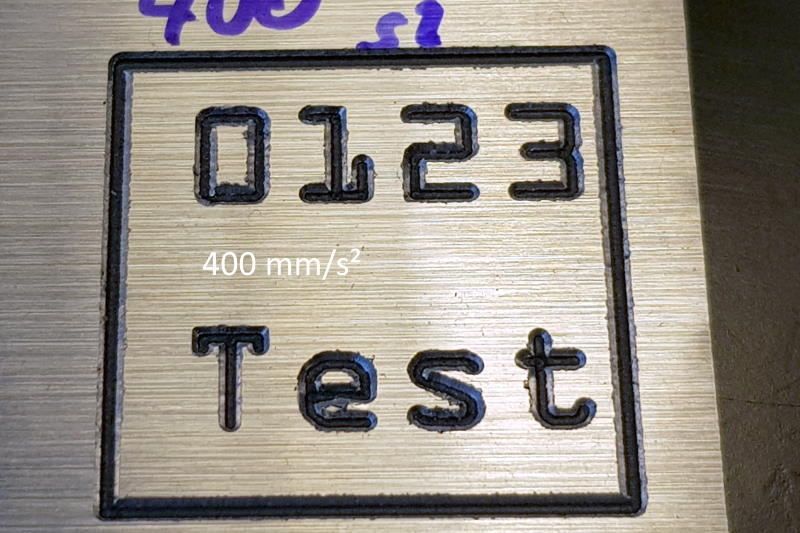
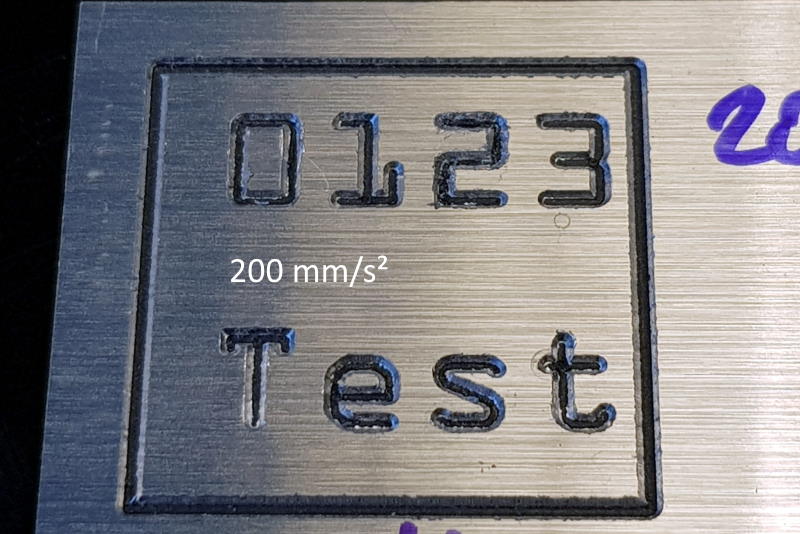
Dieses Experiment zeigt, dass die vertikalen Kerben bei geringerer Beschleunigung deutlich weniger sichtbar werden und unterhalb irgendwann sogar ganz verschwinden. Da ich die Maschine für diese Anpassung stets neustarten musste, waren Werkzeug und Z0-Höhe immer neu einzumessen. Möglicherweise hatte ich ein Staubkorn unter dem Werkzeuglängensensor bei der Vermessung für die geringste Beschleunigung, daher kommt die Gravur hier nicht ganz so gut hervor.
Beleuchten wir kurz, ob die Maschine bei diesen kleinen Strukturen überhaupt die Zielgeschwindigkeit von F1000mm/min
erreichen kann: Die Texthöhe beträgt s0=6mm
, sodass die Maschine bei a=800mm/s²
, etwa t=F/a=20ms
für die Beschleunigung auf den angepeilten Vorschub benötigt. Dabei legt sie eine Distanz von s=a/2*t^2=0.17mm
zurück. Daher wird für s1=6-2*0.17=5.66mm
mit voller Geschwindigkeit verfahren, z.B. für den vertikalen Strich im Buchstaben t
. Hier sind die kinematischen Gleichungen mal wieder sehr nützlich gewesen 😃
Jetzt wäre es noch interessant, die Eigenfrequenz der Maschine in X-Richtung zu bestimmen, denn hier treten die Kerben ja auf. Meine Überschlagsrechnung ergibt: 11
Kerben auf 6mm
Weg bei einer Geschwindigkeit von F1000mm/min --> F16.67mm/s
ergibt fE=30Hz
. Da die Anregung der Maschine in der “Ansteigenden” Halbwelle geschieht, sollte ich stets versuchen, die Maschine weit weg von t=1/(2f) = 16ms
auf Zielgeschwindigkeit zu bringen und so die Resonanzfrequenz vermeiden.
Kurzgesagt: Die kinematischen Parameter sollten - besonders bei weniger steifen und eher leichten Maschinen - fein auf die jeweilige Fräsmaschine angepasst werden. Hierbei it es hilfreich, die Eigenfrequenz der instabilsten Achse zu kennen und “weiträumig” zu umschiffen. Für meine Maschine habe ich festgestellt, dass eine Beschleunigung von a=400mm/s²
noch ausreichend zügig ist, meine Probleme mit am Werkstück sichtbaren Schwingungen aber löst.
Halterung des Fräsmotors
Ich wusste, dass dies bei Überlastung der Maschine ein Problem darstellen würde. Für Gravurarbeiten jedoch fräst die Spindel quasi im Leerlauf. Daher klammere ich diesen Aspekt hier aus.
Unwucht des Fräsers oder der Spannzange
Wenn dies der Fall gewesen wäre, hätte ich ungewöhnliche Geräusche oder Vibrationen der Maschine wahrnehmen müssen. Da dies alles nicht vorlag, schließe ich Unwucht des Werkzeugs als Ursache aus.
Maßnahmen
- Fräser nach Benutzung prüfen und reinigen, bei übermäßigem Verschleiß austauschen.
- Vermeiden von Gleichlauf bei der Verarbeitung von Dibond. Die Gravurpfade lieber minimal weiter auslegen und dann beide Seiten der Gravur im Gegenlauf fertigen.
- Bei höheren Gravurtiefen einen Schlichtgang hinzufügen
- Maschinenbeschleunigung in Verbindung mit Vorschüben bei weniger steifen Maschinen drosseln.
- Vor Einstieg in die Fertigung ein paar Probefräsungen durchführen.
Dieses Teil wurde nach Ausführung der oben genannten Maßnahmen gefertigt.