Vakuumtisch für die CNC
Nehmen wir mal an, Sie sind nicht durch Zufall beim Surfen durch das Internet auf diesen Beitrag gestoßen. Sie wissen also bereits was ein Vakuumtisch ist (falls nicht: hier weiterlesen). Sein Wirkprinzip wird im Bild auf der rechten Seite erläutert. Wahrscheinlich wissen Sie außerdem bereits, dass es verschiedene Typen Vakuumtische für unterschiedliche Zwecke gibt, und vielleicht auch schon, dass Sie einen anschaffen möchten.
Hervorragend! Dieser Artikel beschreibt sowohl meinen eigenen Weg hin zu einem Vakuumtisch, soll aber ebenfalls als Entscheidungshilfe für Sie dienen. Beginnen wir mit einem kleinen Interview.
Warum möchten Sie einen Vakuumtisch haben?
Gleich zu Anfang die wichtigste Frage.
- 🤩 Weil er toll aussieht, eine Menge Gewicht auf die Waage bringt, stabil und teuer ist?
- 😪 Weil Sie keine Lust mehr haben, sich ständig über das richtige Klemmen des Werkstücks Gedanken zu machen?
- 😖 Oder weil Sie bereits ein paar Fräser verschlissen haben beim Versuch durch Klemmen zu fahren?
- 😨 Oder doch weil sich Doppelklebeband als nicht stark genug erwiesen hat und Ihr Werkstück fliegen ging?
- 😎 Professionalisieren Sie Ihr Gewerk vielleicht gerade und Sie versuchen, Produktionszeit einzusparen?
- 😕 Vielleicht ist auch die Qualität Ihrer Werkstücke nach Bearbeitung unzureichend oder Sie haben Probleme, Plattenware plan zu bekommen?
Meine Gründe: Qualität und höhere Fertigungsgeschwindigkeit
Dies hier soll mein Vakuumtisch in den Griff kriegen:
- Bei Gravuren machen nicht vollkommen plan aufliegende Werkstücke mir einen Strich durch die Rechnung, da die Gravurbreite ungleichmäßig wird. Dies ist leider nicht nur auf Holzwerkstoffe beschränkt.
- Momentan arbeite ich mit Anbindungen, um Frästeile in Position zu halten. Meine Frästeile benötigen also manuelle Nacharbeit und die Anbindungen am Werkstück können danach immer noch erahnt werden.
- Wenn ich keine Anbindungen wünsche, muss ich eine “Zwiebelhaut” übrig lassen, kann also nicht ganz durchfräsen. Das macht die Bearbeitung der Rückseite z.B. mit einem Gravurfräser erforderlich, was durch die genaue Positioniererfordernisse viel Zeit in Anspruch nimmt.
- Mit einem Vakuumtisch werden ballige Werkstücke für die Bearbeitung plan gezogen, sodass Probleme ungleicher Gravuren, nicht erwünschter Durchfräsungen usw. behoben sind.
- Unter bestimmten Bedingungen leidet Meine Maschine an Vibrationen, besonders bei Verwendung langer Zweizahnfräser bei großer Tiefenzustellung und größeren Geschwindigkeiten. Das zusätzliche Gewicht und die flächige Kraftverteilung durch den Vakuumtisch könnten dieses Problem lösen.
Welcher Typ Vakuumtisch?
Ok, nun sollten wir herausfinden, welche Art Vakuumtisch sich am besten für Ihren Einsatz und für Ihre Randbedingungen eignet. Vakuumtische sind prinzipbedingt nur dann sinnvoll, wenn Plattenmaterial mit entsprechend großer Oberfläche bearbeitet wird. Zudem sollte das Plattenmaterial nicht zu biegsam oder sehr porös sein - Folien, Gummimatten und Weichschäume beispielsweise können von einem Vakuumtisch kaum gehalten werden, da durch die Fräskräfte angehobene Kanten des Plattenmaterials sofort das Vakuum kollabieren lassen.
Es gibt drei Typen Vakuumtische:
- Rastervakuumtische
- Lochrastervakuumtische
- Vakuumtische mit poröser Oberfläche
Rastervakuumtisch
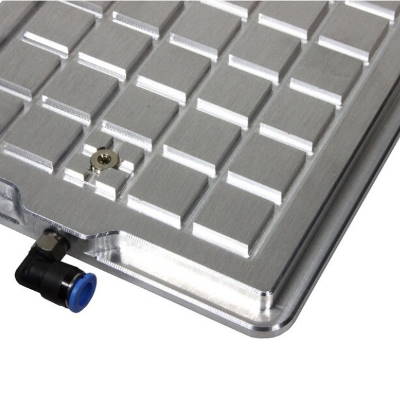
Viele Rastervakuumtische haben nur einen Vakuumanschluss, der in der Mitte des Tisches platziert ist. Der Bereich, in dem Unterdruck das Werkstück halten soll, wird mittels einer in das Raster gelegten (Schaum-) Gummidichtung bestimmt. Hierbei muss sich die Dichtung stets innerhalb des Werkstückes befinden.
Da die Dichtung bei Einschalten des Vakuums zusammengepresst wird und damit Vakuumtisch und Werkstück luftdicht miteinander verbindet, muss die Pumpe nur einen geringen Volumenstrom zur Verfügung stellen. Zudem hält das Werkstück bei entsprechend starkem Unterdruck sehr großen Zug- und Scherkräften stand, ohne sich zu lösen. Durch die flexible Dichtung können auch nicht ganz plan aufliegende Werkstücke oder solche mit rauen Oberflächen auf dieser Art Tisch gut bearbeitet werden.
Bei all den Vorteilen haben sie aber zwei gewichtige Nachteile: Werden erstens verschieden große Werkstücke verarbeitet, ist die Verlegung der Dichtung stets anzupassen. Außerdem muss beachtet werden, dass durch das meist in der Mitte befindliche Absaugloch auch die Werkstücke zentriert werden müssen; Anschläge für das vereinfachte Kantenfinden sind daher oft nicht verwendbar.
Zweitens darf nicht “innerhalb der Dichtung” durchgefräst werden. Tut man es doch, wird das Vakuum sofort zusammenbrechen, da die Pumpe plötzlich einen riesigen Luftstrom bewältigen muss. Daher darf das Werkstück nicht zu klein werden (das Raster ist das Maß der Dinge) oder man muss zusätzlich Arbeit in Klemmen oder Halterungen stecken, die dieses Problem lösen.
Kurzgesagt:
- Rastervakuumtische funktionieren sehr gut, solange man nicht durchfräst.
- Rastervakuumtische stellen geringe Anforderungen an die Pumpe und halten auch unebene oder verzogene Werkstücke sicher.
- Rastervakuumtische sind günstig, benötigen aber bei unterschiedlichen Werkstückgrößen, kleinen Werkstücken oder Durchfräsungen extra angepasste Halterungen.
Lochrastervakuumtisch
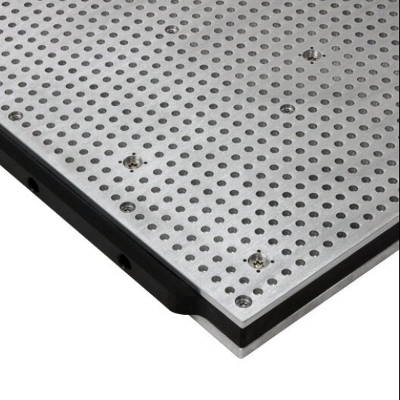
Lochrastervakuumtische verfügen über - wie der Name schon sagt - in einem Raster angeordnete Sacklöcher, über die Luft abgesaugt wird. In jedem dieses Sacklöcher befindet sich eine winzige Durchgangsbohrung, die zu einem im Tisch befindlichen Kanalsystem führt. Der Durchmesser der Durchgangsbohrung wird vom vorrangig zu bearbeitenden Material vorgegeben - sie sind etwas größer bei “porösen” Materialien wie Holz und MDF, und kleiner für die Aluminium- oder Stahlbearbeitung.
Zumeist sind sie in zuschaltbare Segmente unterteilt, sodass bei kleineren Werkstücken nicht der ganze Tisch abgedeckt werden muss um Leckströme zu vermeiden. Dennoch ist es sinnvoll, weiterhin freiliegende Löcher abzudecken und damit den Vakuumdruck zu erhöhen.
Diese Vakuumtische bestehen meist aus drei Teilen: Dem Unterbau zur Montage auf dem Maschinenbett, einer mittleren Ebene mit Vakuumanschlüssen und dem Kanalsystem sowie einer oberen Ebene mit Lochraster, was zudem oft eine Bearbeitungsreserve zum Planfräsen aufweist.
Sie sind in der Lage, Werkstücke jeglicher Form niederzuhalten, vorausgesetzt sie besitzen eine ebene Fläche auf der Unterseite. Die kleinen Durchgangsbohrungen ermöglichen auch das Durchfräsen: die betroffenen Löcher liefern zwar keinen Beitrag mehr zur Klemmkraft, überfordern mit dem geringen Leckstrom aber auch die Vakuumpumpe nicht, sodass sie den Unterdruck bei den anderen Löchern aufrecht erhalten kann (solange man es mit der Anzahl freiliegender Löcher nicht übertreibt). Das Ausrichten des Werkstücks ist auf solchen Tischen ebenfalls einfach, da das Lochraster einfach mit Zentrierstiften bestückt werden kann, die einen Anschlag o.Ä. bilden.
Nachteile dieses Tischtyps sind ihr hoher Preis durch das aufwändige Design, mehr benötigtes Zubehör wie Vakuumverteiler bei einem Mehrkammersystem (und alles muss leckfrei gehalten werden), sowie hohe Anforderungen an die Vakuumpumpe bei Durchfräsungen.
Kurzgesagt:
- Lochrastervakuumtische sind für jedes feste Werkstück mit genügend Oberfläche und glatter Unterseite geeignet.
- Lochrastervakuumtische tolerieren Durchfräsungen und freiliegende Löcher, erfordern dann aber großzügig dimensionierte Vakuumpumpen.
- Lochrastervakuumtische vereinfachen die Positionierung von Werkstücken ungemein.
- Lochrastervakuumtische sind komplex in der Fertigung und daher vergleichsweise teuer.
Vakuumtische mit poröser Oberfläche
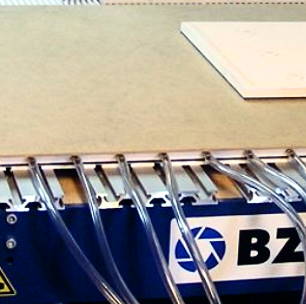
Diese Art Vakuumtisch benötigt weder sichtbare Löcher noch Kanäle an seiner Oberfläche: Stattdessen ist die Oberfläche selbst luftdurchlässig. Für das Fräsen von Leiterplatten wird als Material oft Aluminiumschaum verwendet. Im Hobbybereich gibt es auch gute Erfahrungen mit überplanter mitteldichter Faserplatte. Bei Letzterer ist es beim Durchfräsen nicht einmal schlimm, wenn man sich mit der Materialdicke vertan hat, da MDF solche Fehler gut verzeiht und bei Bedarf einfach eine frische Platte aufgelegt werden kann.
Die Tische sind leicht und - mit viel Hintergrundwissen über Werkstoffe und Dünwwandfräsen - sogar als “Marke Eigenbau” zu fertigen - viele Beispiele hierzu gibt es da draußen im Netz.
Sie funktionieren am besten über einen großen Volumenstrom und arbeiten daher meist mit geringen Unterdrücken - sie erhalten ihre Klemmkraft also über die Fläche. Besser noch als Lochrastervakuumtische sind sie also für Durchfräsungen geeignet. Zudem sind sie in der Anschaffung günstig und können sogar mit Staubsaugern betrieben werden, deren Motoren auch ohne Förderstrom durch ein eigenes Gebläse gekühlt werden.
Ihre Nachteile: Durch ihr geringes Gewicht sind sie anfälliger für Vibrationen. Sie benötigen Werkstücke mit eher großer Oberfläche um adäquate Klemmkräfte zu realisieren und bei hohen Unterdrücken bleibt das poröse Obermaterial nicht maßhaltig, es “schrumpft” also bei aufgelegtem Werkstück etwas. Außerdem sind sie nicht geeignet bei Verwendung von Kühlschmierstoffen und haben einen ungünstigen statischen Reibungskoeffizienten (Je nach Werkstückpaarung bieten sie keinen besonders guten Halt gegen laterale Verschiebung).
Kurzgesagt:
- Porenvakuumtische sind günstig zu erwerben und zu betreiben.
- Porenvakuumtische sind für größere Werkstücke und Materialien, die keine Kühlschmierstoffe benötigen, gut geeignet.
- Porenvakuumtische sind bei Durchfräsungen sehr gut geeignet.
- Porenvakuumtische sind bei Verwendung von MDF nicht präzise in Z-Richtung.
Was alle diese Vakuumtische gemeinsam haben
Die Klemmkraft auf das Werkstück in Z-Richtung kann für einen gegebenen Unterdruck auf identische Art berechnet werden. Aber vorsicht, dieser Unterdruck ist bei Durchfräsungen und anderen Quellen für Leckagen am Werkstück geringer als auf dem Manometer angezeigt.
Werden keine Durchfräsungen gefertigt, lässt sich die volle Werkstückoberfläche zur Berechnung der Klemmkraft hinzuziehen (und nicht nur die Summe der Fläche aller Löcher im Bereich unter dem Werkstück im Falle des Lochrastertisches). Das kommt daher, dass mikroskopisch kleine Unebenheiten auf der Oberfläche von Werkstück und Tisch einen geringen lateralen Luftfluss an der Grenzschicht zulassen.
Andererseits gilt dies auch für die Ränder des Werkstücks. Nutzt man also keinen Rastervakuumtisch, wird es immer Leckageluftströme geben. Fräst man zusätzlich komplett durch das Material, werden weitere Randzonen erzeugt, die wiederum geringere Klemmkräfte aufweisen als der Rest des Werkstücks.
Welches Zubehör für einen Vakuumtisch?
Ohne Pumpe funktioniert der Vakuumtisch natürlich gar nicht. Und obacht, werden hohe Unterdrücke und gleichzeitig große Volumenströme verlangt, bewegt sich der Preis für die gewünschte Pumpe ganz schnell in derselben Liga wie der Vakuumtisch. Aber das führt hier zu weit - ich habe den Vakuumpumpen einen eigenen Artikel gewidmet. Aber es wird weiteres Zubehör benötigt:
- Schrauben, Unterlegscheiben, Nutensteine / Muttern um den Tisch auf der Maschine zu befestigen
- Sortiment verschieden dicker Unterlagsbleche für die plane Montage des Tisches gegenüber der Z-Achse der Maschine
- Einen Vakuumverteiler, falls der Vakuumtisch mehrere Zonen besitzt
- Vakuumleitungen
- Einen Schalter mit Motorschutz für die Vakuumpumpe
- gegebenenfalls ein Vakuumvlies (Holz-, Kunststoffbearbeitung) oder eine Lochrastermatte aus Gummi (Alu, Stahl)
- Dichtband (für Rastervakuumtische)
Zusammenfassung
Alles in allem will die Anschaffung eines Vakuumtisches gut überlegt sein - gerade wegen des großen Kosten- und Zeitaufwandes für Montage, Einrichtung und Betrieb des Tisches. Entscheidet man sich dennoch dafür, so wird man bei zweckmäßigem Einsatz mit höherer Fertigungsqualität durch die flächige Auflage des Werkstücks, kürzerer Richtzeit durch Wegfallen der Klemmen und einfacherer Jobplanung belohnt - denn Materialanbindungen sind nun passé.
Meine Wahl
Ich arbeite ausschließlich mit Plattenmaterial. Ich fertige bisher Produkte aus Holz, Hochdrucklaminaten, Acrylglas, mitteldichter Faserplatte oder Aluminium-Verbundmaterial. Zumeist muss ich Konturen aus einer größeren Platte ausschneiden (Durchfräsen) und wende Nestingverfahren an, um möglichst wenig Abfall zu erzeugen. Ich arbeite oft zweiseitig, was eine genaue Lokalisierung des Werkstückes auf dem Maschinentisch erfordert. Daher kommt ein Rastervakuumtisch für mich nicht infrage.
Um die Kanten auf der Werkstückunterseite anzufasen, schneide ich im ersten Arbeitsgang meist nicht ganz durch, sondern lasse einen V-Fräser diesen letzten Schritt auf der Unterseite erledigen. Da ich hierfür eine sehr exakte Bestimmung der Werkstückhöhe benötige und der Unterdruck sich bei Auffräsen einer Kontur durch den Fasenfräser verringert, muss die Oberfläche des Vakuumtisches starr sein - daher kommt ein Porenvakuumtisch mit Oberfläche aus MDF für mich nicht in Frage.
Stattdessen habe ich einen Hersteller für Vakuumtische direkt kontaktiert, um ein paar kleine Lochrastervakuumtische zu kaufen, die ich unabhängig voneinander einschalten und damit je nach Größe des Werkstücks Segmente auf meiner CNC mit Unterdruck versorgen könnte. Dieser meinte, dass die einfachere und bessere Lösung ein für meine Maschine angepasster Vakuumtisch sei, da bei Zusammenstellen mehrerer Tische Höhenunterschiede und Undichtigkeiten entstehen würden und die Zuführung der Vakuumleitung erschwert würde.
Also habe ich gespart und mir den teureren, großen Tisch zugelegt. Hierfür habe ich dem Hersteller Zeichnungsdaten meiner Maschine zur Verfügung gestellt und nach ein paar Gesprächen und Vorschlägen seitens des Herstellers hatte ich dann einen an meine Bedarfe angepassten Entwurf.
Lieferung des Tisches
Der von mir ausgewählte Hersteller sitzt nicht zu weit von meinem Wohnort entfernt. Also bin ich hingefahren für eine kleine Führung durch die Produktion und konnte den Tisch dabei direkt mitnehmen. Da ich für die Montage meine alte Werkstückunterlage vom Maschinentisch nehmen musste, konnte ich in einem Zug direkt Schalldämmung im Maschinenrahmen anbringen. So wird die Maschine nochmal etwas leiser.
Danach habe ich den Vakuumtisch mit M6 Maschinenschrauben und T-Nut Muttern am Rahmen befestigt. Für eine ebene Oberfläche (gemessene Abweichung in Z über die gesamte Fläche des Maschinentisches unter 15/100mm
, Messuhr siehe Bild unten links) habe ich Unterlegbleche verwendet und stundenlang nachkontrolliert und -justiert, bis ich zufrieden war.
Für noch bessere Ergebnisse könnte man:
- Den Vakuumtisch einmal komplett planfräsen
- Dn Tisch wieder herunternehmen und den Maschinenrahmen so nachrustieren, dass die Profile exakt waagerecht aufliegen und die Oberseiten aller Rahmenteile auf das Hundertstel genau auf einer Ebene enden.
Dies erschien mir als unverhältnismäßig großer Aufwand angesichts der vorhandenen Maschinentoleranzen (Immerhin handelt es sich hier um einen Eigenbau), also gebe ich mich mit den oben erreichten Werten zufrieden.
Anschluss des Vakuumverteilers
Als ich einfach drauflos die dünnen Vakuumleitungen zur Verbindung von Tisch und Verteile zurechtschnitt, dachte ich mir: “Warte mal eine Sekunde. Wäre es nicht klüger, die 9mm-Leitungen so kurz wie möglich zu halten, und lieber die 18er-Leitung zur Pumpe länger zu lassen und so den Druckabfall zu reduzieren?” Also habe ich mich erst einmal mit dem Taschenrechner zurückgezogen.
- Mein Tisch hat etwa 4900 Sauglöcher mit je
0.5mm
Durchmesser. Ihre zusammengerechnete Oberfläche beträgt \(A_{table}=962mm²\), was in etwa einem Loch mit35mm
Durchmesser entspricht (ich ignoriere hier komplett die Widerstände an den Lochrändern.) - Die sieben Vakuumleitungen zum Verteiler haben einen Durchmesser von
9mm
. Zusammengenommen liegt ihre Oberfläche bei \(A_{hose}=445mm²\), entsprechen also einem Loch mit24mm
Durchmesser; deutlich weniger also als der Gesamtquerschnitt der Löcher des Tisches. - Für den Saugschlauch mit
18mm
Innendurchmesser sieht es sogar noch schlimmer aus: \(A_{pump}=254mm\) liegt bei unter 30% des Querschnitts auf dem Tisch.
Wenn ich jetzt also von einem gleichmäßigen Leckagestrom über die sieben Segmente meines Tisches ausgehe, macht es Sinn, die Pumpenzuleitung so kurz wie möglich zu wählen, da sie bei vielen offenen Sauglöchern die höchste Flussgeschwindigkeit und damit den höchsten Druckverlust aufweist. In einem Szenario mit weniger verwendeten Segmenten wird irgendwann die 9mm-Leitung ausschlaggebend.
Daher ist also zu beachten, dass das Manometer am Vakuumverteiler bei größeren Leckageluftströmen einen höheren Wert anzeigt, als am Tisch tatsächlich anliegt!
Da ich die Zahl freiliegender Löcher aber begrenzen werde, kann ich mir einfach eine komfortable Position für den Vakuumverteiler aussuchen und die Verlegung abschließen 😉. Übrigens ist das erste auf meinem neuen Vakuumtisch gefertigte Teil ein Halter für den Vakuumverteiler aus Holz - wie im Bild rechts zu erkennen.